Accurate temperature measurements are essential for the proper monitoring and control of industrial furnaces. However, measurement uncertainty is a risk for such a critical parameter. Certain instrumental and environmental errors must be considered when using spectral-band radiation thermometry techniques, such as the uncertainty in the emissivity of the target surface, reflected radiation from surrounding objects, or atmospheric absorption and emission, to name a few.
Undesired contributions to measured radiation can be isolated using measurement models, also known as error-correction models. This paper presents a methodology for budgeting significant sources of error and uncertainty during temperature measurements in a petrochemical furnace scenario. A continuous monitoring system is also presented, aided by a deep-learning-based measurement correction model, to allow domain experts to analyze the furnace’s operation in real-time.
To validate the proposed system’s functionality, a real-world application case in a petrochemical plant is presented. The proposed solution demonstrates the viability of precise industrial furnace monitoring, thereby increasing operational security and improving the efficiency of such energy-intensive systems.
Date |
Apr 2021
Tags |
#machine learning
#energy
#measurement
#temperature
#radiation
#thermometry
#industry
#optimization
#neural network
Technologies |
python
·
numpy
·
matplotlib
·
r
·
latex
·
tikz
·
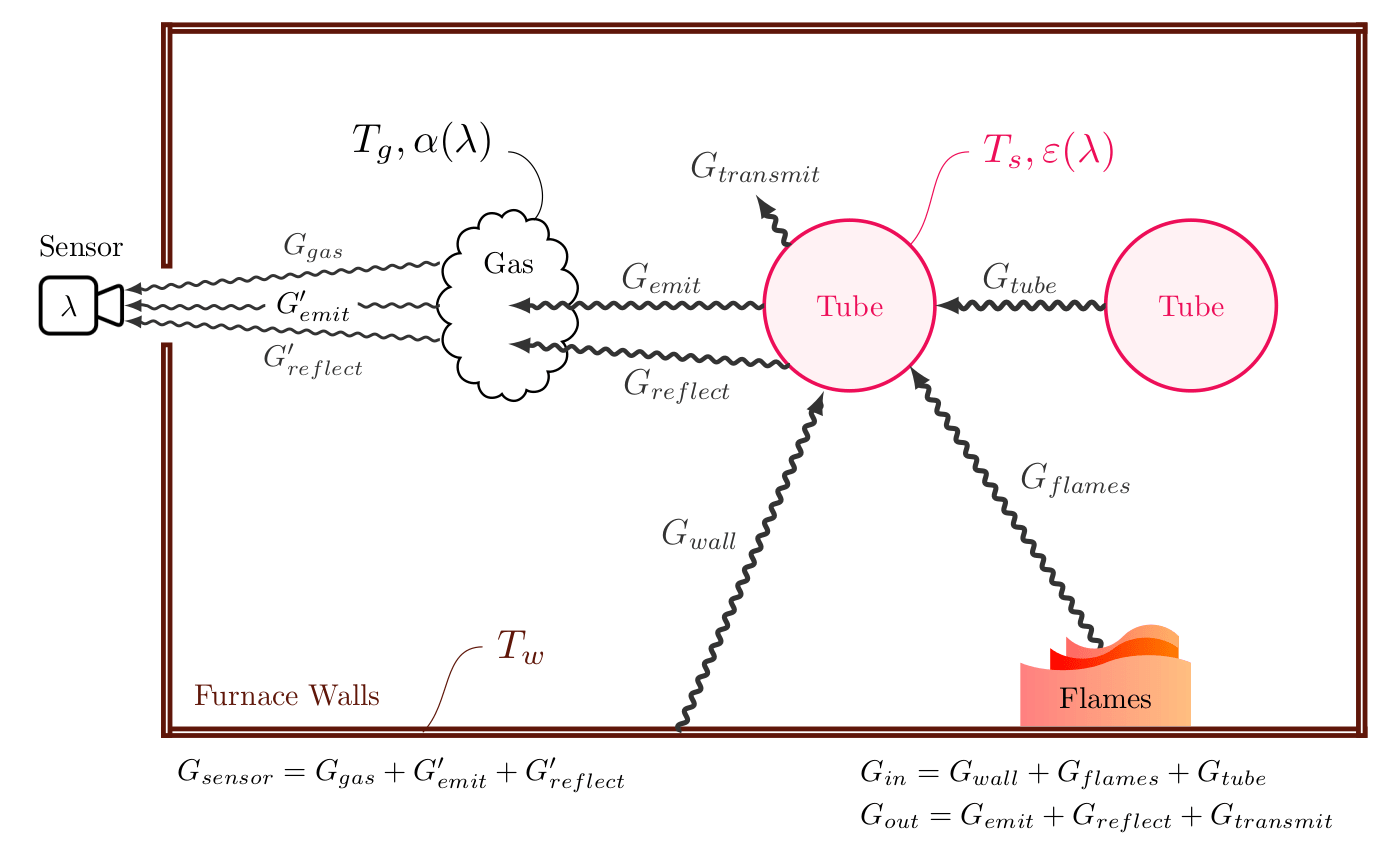
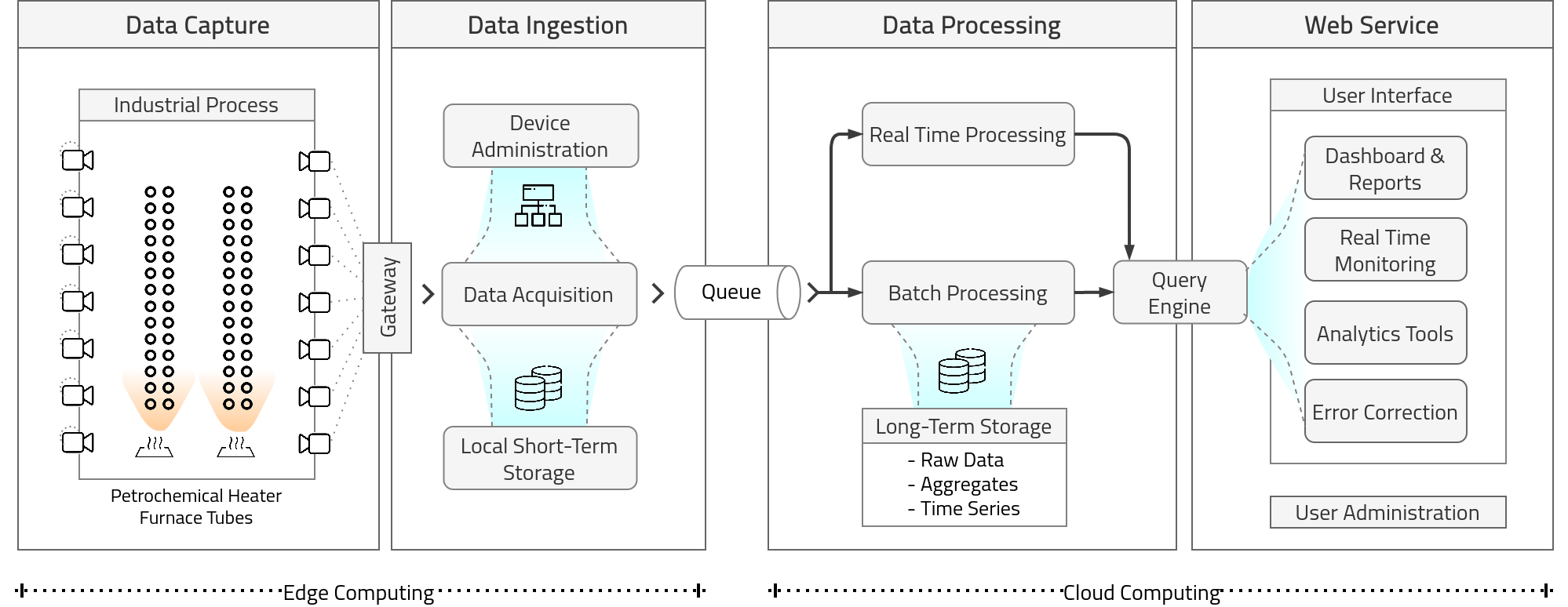
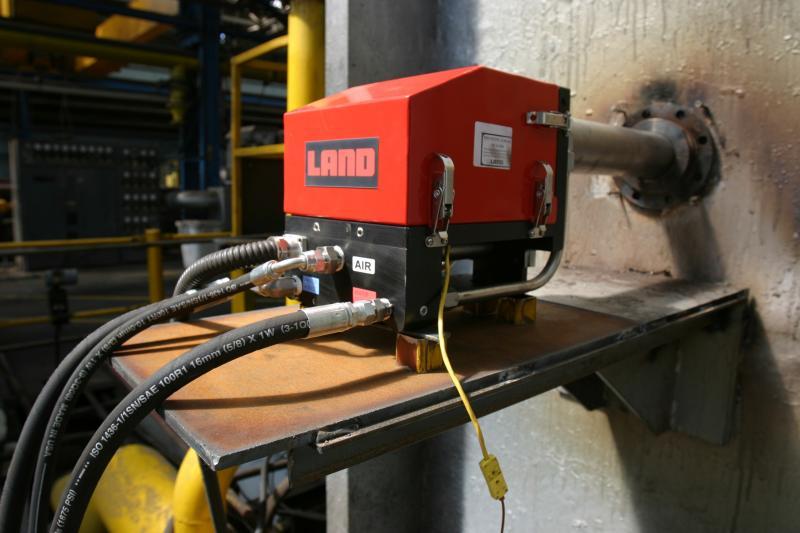
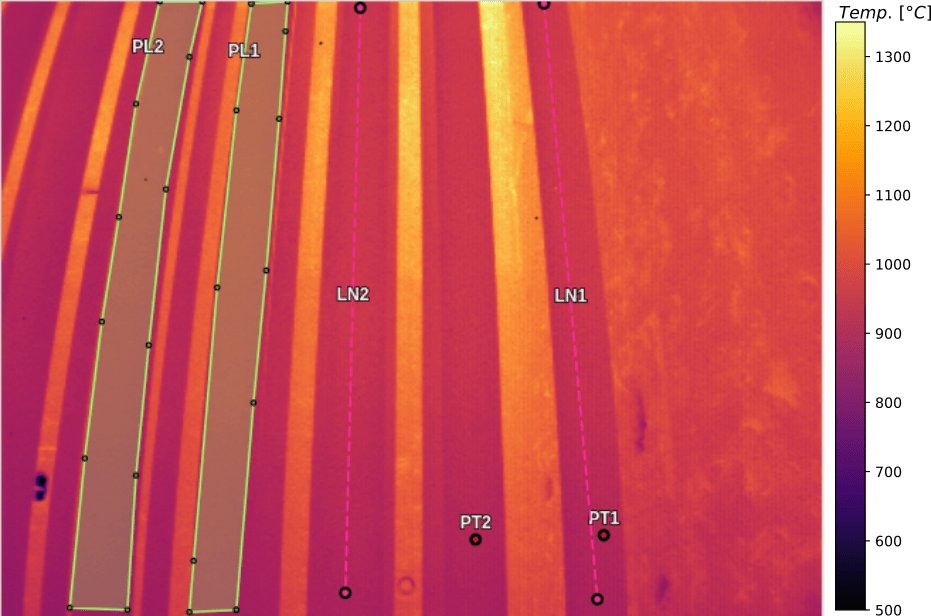